1756 if16 user manual
Summary
Don’t pull your hair out! Find the 1756 IF16 user manual at Jayasinha.com. Your guide to conquering the IF16 is here! Download now!
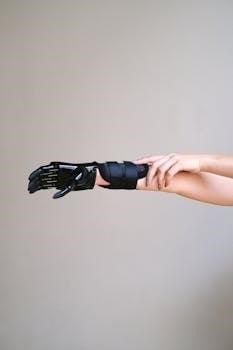
Overview of the 1756-IF16 Analog Input Module
The 1756-IF16 is an Allen-Bradley ControlLogix analog input module designed for converting analog signals into a digital format‚ enabling processing by programmable logic controllers․ It offers a 16-channel capacity for voltage inputs‚ typically ranging from -10V to 10V‚ and current inputs‚ usually from 4mA to 20mA․
Key Features of the 1756-IF16
The 1756-IF16 analog input module boasts several key features․ These include its sixteen channels‚ accommodating both voltage and current input signals․ It supports differential and single-ended input configurations․ This module provides wire-off detection‚ alerting users to signal interruptions‚ enhancing system reliability․ It is designed for use within ControlLogix systems․
Number of Channels
The 1756-IF16 analog input module from Allen-Bradley is primarily characterized by its capacity to handle a significant number of input channels․ Specifically‚ this module is equipped with 16 individual channels‚ making it a high-density solution for applications requiring multiple analog signal measurements․ These channels can be configured to receive various types of analog signals‚ such as voltage or current‚ depending on the specific application requirements․
The availability of 16 channels in a single module reduces the overall system footprint and simplifies wiring compared to using multiple modules with fewer channels․ This high channel density is particularly beneficial in applications where space is limited or where minimizing wiring complexity is crucial․
Each of the 16 channels functions independently‚ allowing for simultaneous monitoring of multiple analog signals․ This capability is essential in applications where real-time data acquisition and processing are required․ The module’s ability to handle multiple inputs concurrently ensures that no data is missed and that the control system has a complete and up-to-date view of the process being monitored․
Furthermore‚ the 16 channels can be configured individually or in groups‚ providing flexibility in adapting the module to different application scenarios․ This configurability allows users to optimize the module’s performance and tailor it to their specific needs․
Input Signal Types
The Allen-Bradley 1756-IF16 analog input module is engineered to accommodate a versatile range of input signal types‚ enhancing its adaptability to diverse industrial applications․ Primarily‚ it supports both voltage and current inputs‚ catering to the most commonly used analog signals in automation and process control systems․
For voltage inputs‚ the 1756-IF16 typically handles signals ranging from -10V to +10V․ This voltage range is suitable for interfacing with various sensors and transmitters that output voltage signals proportional to the measured process variable․ The module’s ability to accept both positive and negative voltages allows for measuring bipolar signals‚ which are often encountered in applications involving differential measurements or signals that fluctuate around a zero point․
In addition to voltage inputs‚ the 1756-IF16 also supports current inputs‚ typically in the range of 4mA to 20mA․ This current loop is a widely adopted standard in industrial instrumentation due to its inherent noise immunity and ability to transmit signals over long distances without significant signal degradation․ The 4mA value represents the zero or minimum value of the measured variable‚ while the 20mA value corresponds to the full-scale or maximum value․
The module’s capability to handle both voltage and current inputs makes it a versatile choice for a wide array of applications‚ eliminating the need for separate modules for different signal types․ This flexibility simplifies system design‚ reduces hardware costs‚ and streamlines maintenance․
Differential and Single-Ended Inputs
The Allen-Bradley 1756-IF16 analog input module provides the flexibility of both differential and single-ended input configurations‚ catering to different application requirements and signal integrity considerations․ Understanding the distinction between these configurations is crucial for proper wiring and optimal performance․
Differential inputs measure the voltage difference between two input terminals‚ effectively rejecting common-mode noise․ This configuration is particularly beneficial in environments with high electrical noise or when dealing with long signal cables‚ as it minimizes the impact of induced noise on the measurement accuracy․ By measuring the difference between the two signals‚ any noise that is common to both wires is canceled out‚ resulting in a cleaner and more reliable signal․
Single-ended inputs‚ on the other hand‚ measure the voltage difference between a single input terminal and a common ground reference․ This configuration is simpler to wire but is more susceptible to noise‚ as any noise present on the ground reference will be directly added to the measured signal․ Single-ended inputs are generally suitable for applications where the signal source is located close to the module and the environment is relatively noise-free;
The 1756-IF16 module allows users to configure individual channels for either differential or single-ended input‚ providing maximum flexibility in adapting to different sensor types and application scenarios․ When using differential inputs‚ it’s essential to connect both the positive and negative signal wires to the appropriate terminals on the module․ For single-ended inputs‚ only the signal wire needs to be connected‚ with the ground reference being shared among all channels․
Wiring Instructions for the 1756-IF16
Proper wiring is crucial for optimal performance․ Refer to the Allen-Bradley manual for detailed instructions․ Ensure correct polarity and grounding to prevent damage․ Use appropriate wire gauges and terminal blocks for secure connections․ Always de-energize power before wiring․
Wiring a 3-Wire Transmitter
Wiring a 3-wire transmitter to the 1756-IF16 analog input module requires careful attention to ensure proper signal transmission and accurate readings․ The 3-wire configuration typically involves a power supply wire‚ a signal wire‚ and a common ground wire․ Begin by identifying the appropriate terminals on both the transmitter and the 1756-IF16 module‚ consulting the respective user manuals for specific pinouts and wiring diagrams․
Connect the transmitter’s power supply wire to the designated power supply terminal on the 1756-IF16 module‚ ensuring that the voltage matches the transmitter’s requirements․ Next‚ connect the transmitter’s signal wire to the appropriate analog input channel on the 1756-IF16 module․ This wire carries the analog signal representing the measured process variable․
Finally‚ establish a common ground connection between the transmitter and the 1756-IF16 module․ This connection provides a reference point for the signal and power supply‚ minimizing noise and ensuring accurate signal transmission․ Double-check all connections to verify that they are secure and properly insulated․ Incorrect wiring can lead to inaccurate readings‚ signal noise‚ or even damage to the equipment․ After wiring‚ thoroughly test the system․
Wiring for Current Input
When wiring the 1756-IF16 module for current input‚ it’s essential to follow proper procedures to ensure accurate and reliable measurements․ The 1756-IF16 module supports current input signals‚ typically ranging from 4mA to 20mA‚ commonly used in industrial automation for transmitting process variables․ Begin by identifying the specific channel on the 1756-IF16 module designated for current input․ Refer to the module’s documentation for the correct terminal assignments․
Next‚ connect the positive (+) wire from the current source to the positive (+) terminal of the selected channel on the 1756-IF16 module․ Similarly‚ connect the negative (-) wire from the current source to the negative (-) terminal of the same channel․ It is crucial to maintain polarity to avoid incorrect readings or damage to the module or the connected device․
Ensure that the current loop is properly completed․ The 1756-IF16 module requires a complete current loop for accurate measurements․ Double-check all connections to confirm they are secure and properly tightened․ Loose connections can introduce resistance and affect the signal integrity․ After wiring‚ calibrate and configure the module appropriately using the software to match the expected current range․ Finally‚ test and verify that the system functions correctly․
Wiring for Voltage Input
Proper wiring for voltage input on the 1756-IF16 module is crucial for accurate and reliable data acquisition․ The 1756-IF16 module supports voltage input signals‚ typically ranging from -10V to +10V‚ and careful attention to wiring is essential for optimal performance․ First‚ identify the appropriate channel on the 1756-IF16 module designated for voltage input․ Consult the module’s documentation for the correct terminal assignments and polarity․
Next‚ connect the positive (+) wire from the voltage source to the positive (+) terminal of the selected channel on the 1756-IF16 module․ Similarly‚ connect the negative (-) wire from the voltage source to the negative (-) terminal of the same channel․ It is crucial to maintain proper polarity to prevent damage to the module or inaccurate readings․
Ensure that the voltage source is within the specified input range of the 1756-IF16 module․ Exceeding the voltage limits can cause damage to the module․ Verify that all connections are secure and properly tightened to prevent signal loss or interference․ Loose connections can introduce noise and affect the accuracy of the voltage readings․ After wiring‚ calibrate and configure the module appropriately using the software to match the expected voltage range․ Test and verify the system functions correctly․
Configuration of the 1756-IF16 Module
Configuring the 1756-IF16 module involves several steps within the Rockwell Automation software environment‚ typically using Studio 5000 Logix Designer․ The configuration process ensures the module operates correctly and provides accurate data to the ControlLogix system․ Start by adding the 1756-IF16 module to the I/O configuration tree in Studio 5000․ This requires specifying the slot where the module is physically installed in the ControlLogix chassis․
Next‚ define the module’s properties‚ including the input signal types for each channel․ The 1756-IF16 supports various input types‚ such as voltage (e․g․‚ -10V to +10V) and current (e․g․‚ 4mA to 20mA)․ Specify the appropriate input type for each channel based on the connected sensors or devices․ Configure the data format‚ resolution‚ and filtering options to optimize the module’s performance for the specific application requirements․ Adjust the scaling and engineering units to represent the data in a meaningful format․
Set alarm and diagnostic settings to monitor the module’s health․ Define thresholds for high and low alarm limits‚ and configure diagnostic parameters to detect wiring faults or sensor failures․ Apply configuration changes‚ and ensure that the system functions correctly․
Troubleshooting the 1756-IF16 Module
Troubleshooting the 1756-IF16 analog input module requires a systematic approach to identify and resolve potential issues․ Start by checking the module’s status indicators for any error codes or fault conditions․ Consult the user manual to interpret these codes and understand the nature of the problem․ Verify the power supply to the module and ensure it meets the required voltage and current specifications․
Inspect the wiring connections to the module‚ ensuring they are secure and correctly wired according to the wiring diagrams in the manual․ Use a multimeter to check the input signals from the connected sensors or devices․ Verify that the signals are within the expected range and that there are no open circuits or short circuits in the wiring․
Review the module’s configuration in the PLC program to ensure it matches the physical wiring and sensor types․ Check for any conflicting settings or incorrect scaling parameters․ Use diagnostic tools in the PLC programming software to monitor the module’s input values and identify any anomalies․
If problems persist‚ consider replacing the module with a known working module to determine if the issue is with the module itself․ Consult the Rockwell Automation support resources or contact a qualified technician for further assistance․